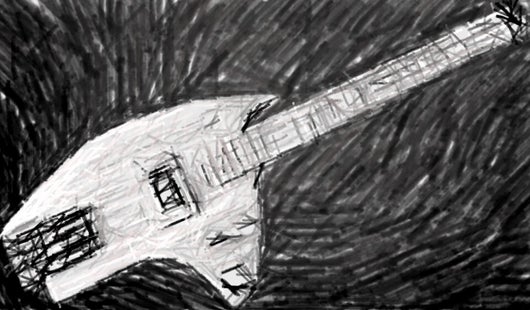
Wie ein Kolibri Buzz nach Kundenanforderung entsteht
Spezifiziert wurde ein Bass mit folgenden Wünschen:
- Body aus Bubinga, Beistellung, knapp 40 mm dick
- Hals aus Mahagoni mit Neusilber-Bünden in eher kräftig ausgeführtem C-Shape
- Griffbrett aus Apfel
- Handstopp an der Halsunterseite auf Höhe des Nullbunds
- Mittels Heavy-Duty-Schalter seriell-parallel schaltbarer Duesenberg Bass-Bucker
- Hardware soweit möglich in silber / Nickel
- Duesenberg Multi Lock Strapper
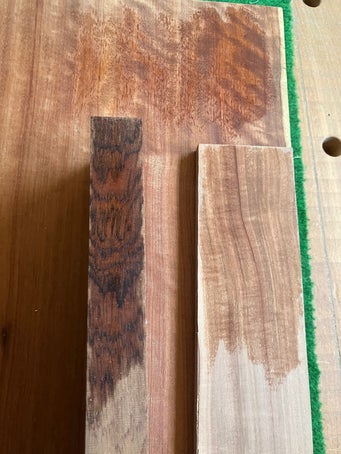
Hier ist die Holzauswahl, zur Probe mit Alkohol angefeuert.
Bubinga Body, Mahagoni Hals, Apfel Griffbrett.
Das Bubinga ist mal richtig schwer ...
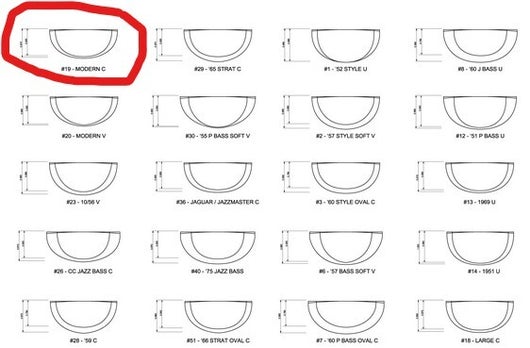
Anhand einer Übersicht mit Halsprofilen wurde Modern C ausgewählt, von der Dicke her Richtung Large C: 22 mm am 1. Bund, 23,5 mm am 12. Bund.
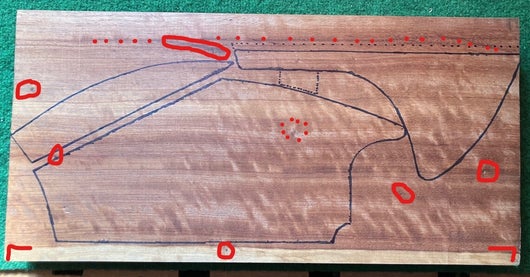
Das Bubinga ist wunderschön geflammt, hat jedoch ein paar Äste, Verfärbungen, einen Mikro-Riss und Splintholz. Das alles konnte umschifft werden.
Der einzige verbliebene Ast im Body wird später vom Kolibri Coin überdeckt.
Aus dem Rest unten rechts lässt sich noch der E-Fach-Deckel gewinnen.
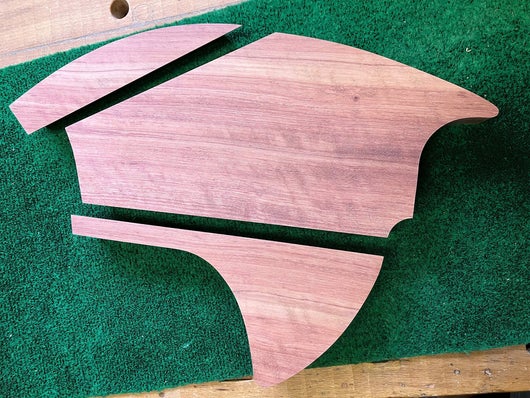
Hier die Einzelteile des Bodys.
Alle Oberflächen wurden vorgeschliffen auf 240. In den Radien habe ich das Hirnholz nass ! gemacht, damit es dabei nicht schwarz wird.
Jedes Werkzeug wird an diesem Holz heiß, selbst Schleifpapier beim Handschliff.

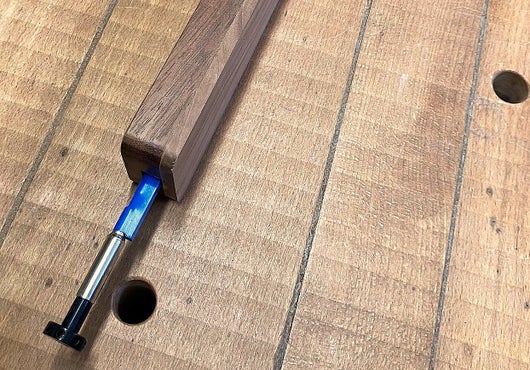
Als nächstes wurde der Hals im Rohbau hergestellt. Es ist eins der Mahagoni Sahnestücke mit senkrechten, feinen Jahresringen.
Der Halsstab ist übrigens entnehmbar. Das erleichtert die Handhabung bei der Weiterbearbeitung, und er kann bei Bedarf ersetzt werden.
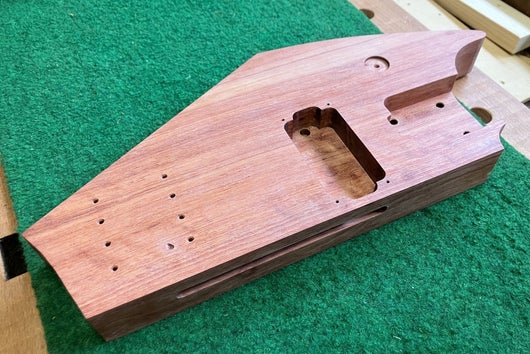
Das Mittelteil ist fertig - die Aussparung für die Tuner kommt erst nach dem Anbau der Wings.
Jetzt kommen das E-Fach und der E-Fach-Deckel dran, anschließend wird der Body zusammengebaut.
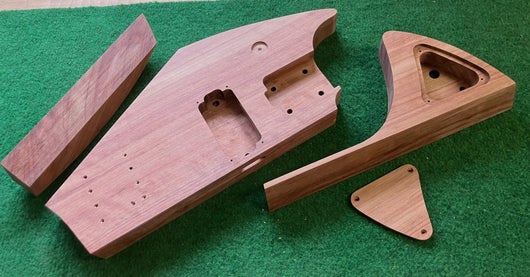
Die fertigen Bauteile vor dem Fügen.
In diesem Fall begleitet von einem "Uff", weil alles problemlos geklappt hat, denn das Holz war ja beigestellt und ist aufgrund der zwischenzeitlichen Handelsbeschränkungen bei einem Fehler kaum zu ersetzen.
Die letzten Bearbeitungen am Body sind eher unkritisch: die Bohrung zum E-Fach und die Aussparung für die Tuner.
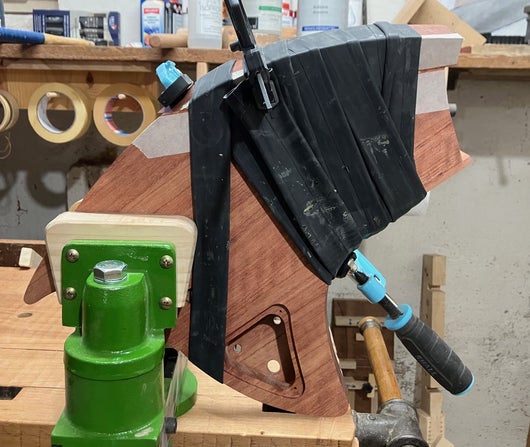
Das Richtfest, so nenne ich den Anbau der Wings, hier der obere, der untere ist schon fest.
Als Druckmittel dient Fahrradschlauch, denn Zwingen ansetzen ist nur eingeschränkt möglich.
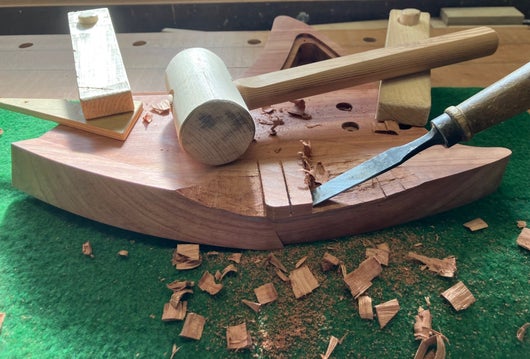
Der Bass hat einen Arbeits-Namen bekommen, und zwar Lithos, für Stein.
Beim Herstellen der Bauchmulde dachte ich nämlich an "abmeißeln", nicht etwa an stemmen, oder gar schnitzen.
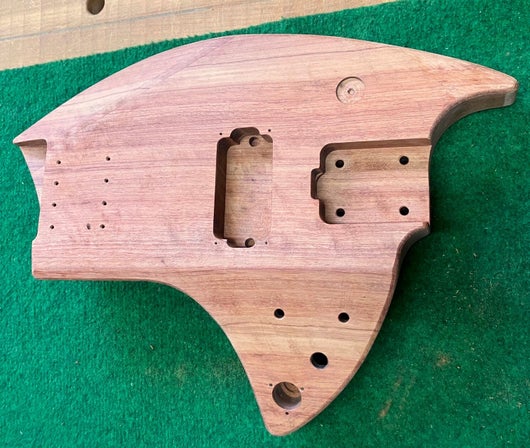
Beim Bohren des Kabelkanals von der Humbuckertasche zum E-Fach musste der -scharfe- Bohrer 2x in Wasser gekühlt werden. Auf 5 cm.
Sagte ich schon dass das Holz hart ist?
Wenn es mal kein Alu mehr gibt, ersetzen wir es durch Bubinga.
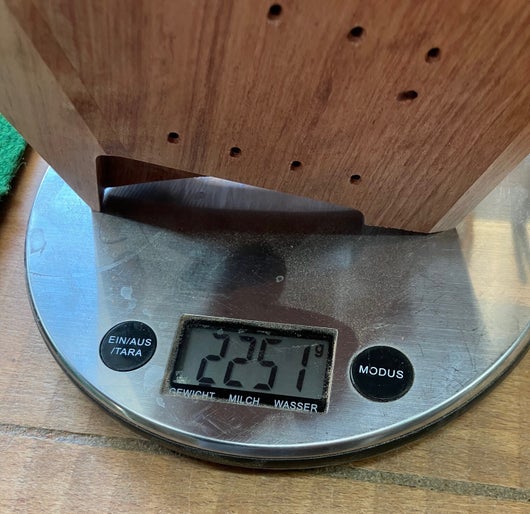
Von der Haptik und dem allgemeinen Feeling her ist der Body sagenhaft.
Er wiegt über 2,2 kg.
Zum Vergleich: Ein Body aus Ahorn wiegt bei gleicher Dicke etwa 1,3 kg, ein Body aus Wildeiche, das schwerste was ich seither hatte, wiegt knapp 1,6 kg.
Also ja, Lithos passt schon.
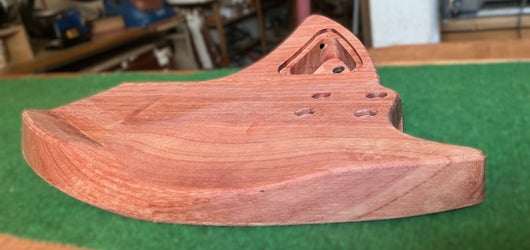
Noch nicht herausgeputzt schon was Besonderes.
Er wird nachdunkeln / braun werden.
Jetzt geht es an die erste Ölung des Bodys,
und an den Hals, seitens Holzbearbeitung vergleichsweise quasi Kindergarten.
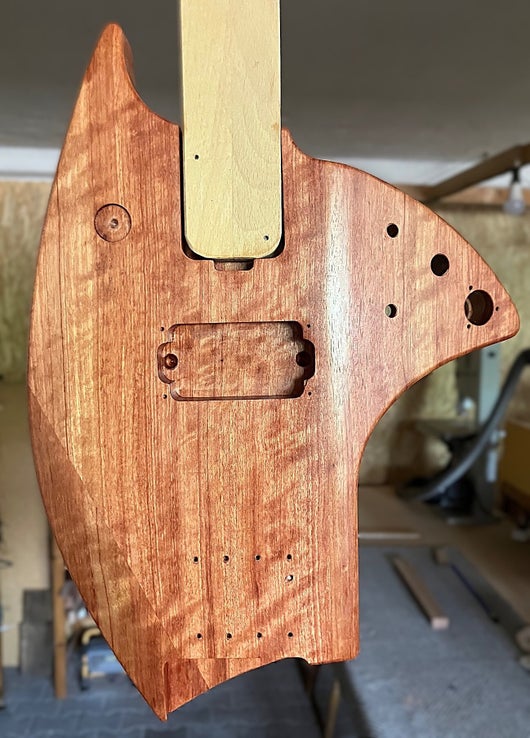
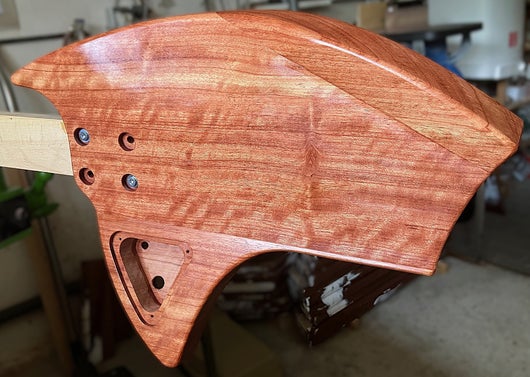
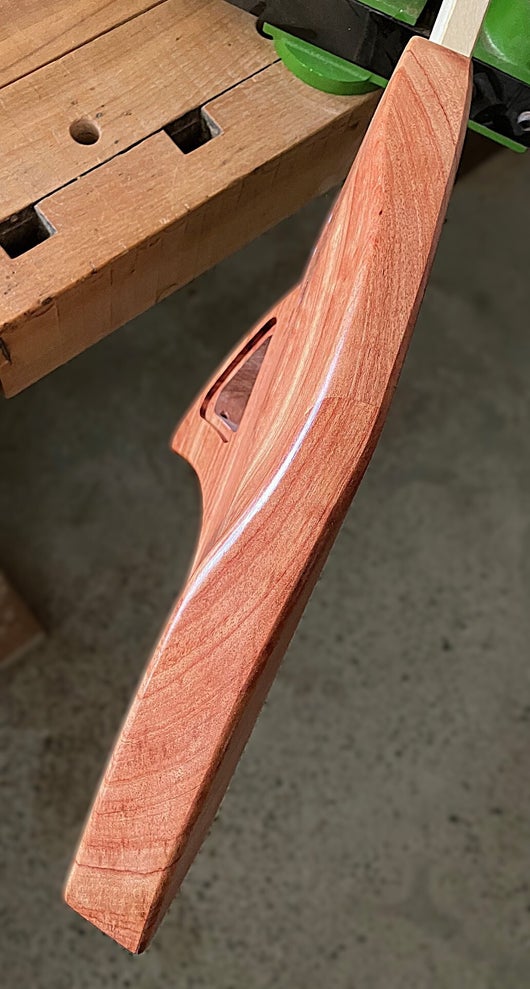
Die erste Ölschicht ist einer der schönsten Momente beim Gitarrenbau, wenn das Holz wieder zum Leben erwacht und zeigt was es kann ...
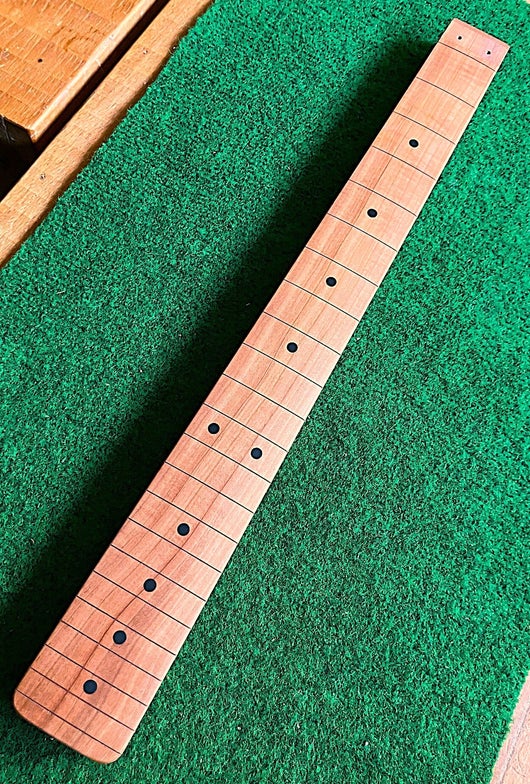
Das Griffbrett ist fertig für die Bundierung.
Farblich passt es super zum Body.

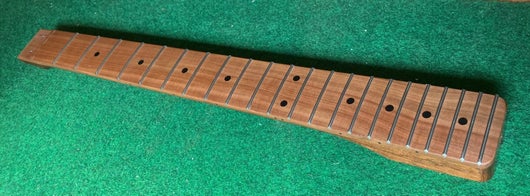
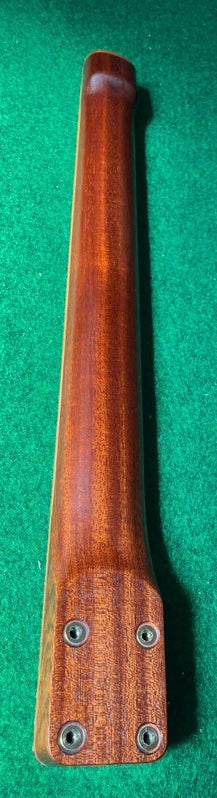
Der Hals ist bundiert und fertig geformt.
Auf Wunsch wurde ein Handstopp / eine Volute angeformt.
Gefüllert und und ein mal geölt zeigt sich das 50 Jahre alte Honduras-Mahagoni von seiner schönsten Seite.
Als nächstes fogt die Verrundung der Bundenden und das Abrichten und Polieren der Bünde.
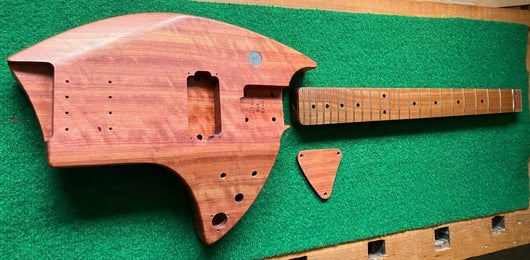
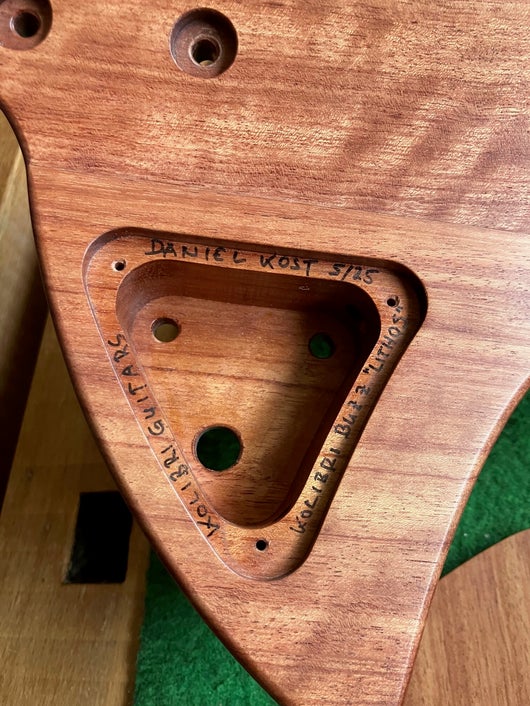
Body, Hals und Bünde sind fertig poliert und bereit zur Montage.
Erstelle deine eigene Website mit Webador